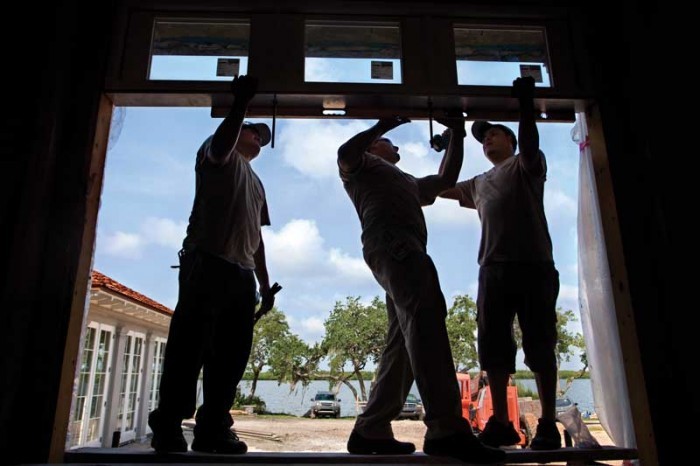
VERO BEACH — Richard Reinhardt, vice president and sales manager at impact resistant window and door company HBS Inc., says the onset of hurricane season doesn’t stir up much extra business.
“It takes six to eight weeks to get these windows made after they are ordered, so people can’t just rush out and have them installed when a big storm starts to form in the Caribbean,” he says.
On the other hand, most windows that go into new and remodeled buildings throughout the year in Vero Beach are designed to withstand the high winds and flying debris generated by hurricanes.
“I’d say 90 percent of the windows we install are impact resistant,” says Reinhard, who got into the window business at just the right time.
Trained as an engineer at Central Florida University, he went to work at his father-in-law’s Vero Beach glass company in the early 1990s, shortly before building code requirements for windows changed dramatically.
“Hurricane Andrew, which I think was in 1992, was the beginning of impact resistant window requirements,” Reinhard says.
According to “Florida Hurricanes and Tropical Storms” published by University Press of Florida, 90 percent of Dade County homes suffered major damage, and 117,000 homes were destroyed during Hurricane Andrew – one of only three category 5 storms ever to make landfall in the U.S.
In response, Dade County building officials developed a new building code that required houses and commercial buildings to be much more wind resistant, starting with roofs and windows.
“Dade County adopted its impact code in 1994 and the state revised its code to more or less match Dade’s in 2001,” Reinhard says. “That new code took effect in Indian River County in 2002.”
Windows, which had been a fairly straightforward commodity, suddenly became a much more technical product, and the business of installing them in custom homes and other challenging applications became an endeavor where the abilities of a structural engineer were needed.
The Indian River County Building code now requires all windows and doors installed in new construction and remodeling to be impact resistant and able to withstand the pressure of 140 mph winds. That can be achieved by the use of standard windows installed with hurricane shutters, or by using windows with impact glass.
“Impact glass is basically two layers of glass with a polyvinylbutyral layer in between,” Reinhard says. “The glass has to be heated to melt the poly somewhat and fuse the sheets of glass together.”
Impact glass can be as thin as 5/16 of an inch for small openings or as thick as 5/8 of an inch for a large opening, and has to be able to withstand a direct hit by a 9-pound 2 by 4 traveling 34 miles an hour.
Glass is just part of the equation. Frame strength, sealant quality and window installation are all equally critical and combine in an endless variety of formulas to achieve the wind and water resistance that is now required by the State of Florida Building Code.
“It has become a real science,” Reinhard says. HBS buys windows from a range of manufacturers to meet the specifications of architects and custom builders who are the company’s main clients.
But all the windows have to meet the same standards to receive a Florida State Product Approval.
“The companies hire outside engineers to design the windows and then test them in a very violent way,” Reinhard says. “They shoot 2-by-4s at them from an air gun and subject them to high pressure and water tests in independent laboratories. The labs then supply the test results to the company engineers who submit their specifications and installation instructions, along with the certified test results, to the state to get a product approval.”
Building inspectors receive product specification sheets from contractors and use those to check window certification and installation when they do the framing inspection on a new or remodeled building.
“You have to use a certain type of screw or concrete anchor spaced according to the plan for the window to perform as designed,” Reinhard says.
Reinhard’s engineering expertise comes in handy when he has to figure out ways to make the state-approved windows perform in custom applications, such as window walls.
If a single window is installed in a solid wall, all that’s required is proper fastening and sealing. But if half a dozen windows are grouped together Reinhard has to work with the architect and builder to come up with a way to make the installation structurally strong enough to withstand the force of a hurricane while achieving the look the architect is after.
Founded in 1973 by retired New York City police detective John Barrie, HBS installs windows along a stretch of coast from Brevard to Palm Beach counties.
Despite the state-wide drop-off in construction, HBS enjoys a steady supply of work thanks to well established industry relationships, according to Reinhard.
“Most of our work is repeat business with architects and builders we have done multiple jobs for already,” he says. “By dealing with us they know they are getting quality products and quality installation along with topnotch service. This is our specialty and we take it very seriously. Builders know if they hand the project off to us, that’s one thing they don’t have to worry about. We provide single-source accountability for them and their clients.”
“HBS is a fantastic company,” says Robert Paugh, general manager of Bill Bryant & Associates Construction Company. “They replaced all the windows in 49 buildings at Vista Plantation for us in 2008, which was a $4.5 million job, and I can’t tell you how any letters I’ve received from residents complimenting their work. They delivered superior quality and exceptional workmanship.”
Other notable HBS projects include installing the windows at the Quail Valley River Club, the Moorings Country Club, the Orchid Beach condos and the Royal Palm Pointe condos.